Missão quase impossível Simplicidade e sustentabilidade foram algumas das lições aprendidas nas empresas Parecia uma missão impossível visitar o Japão apenas seis me-ses após o maior terremoto já registrado na história do país – 8,9 graus na escala Richter – e que gerou um tsunami de dez metros que, além de destruir as cidades litorâneas pró-ximas ao epicentro, ainda causou um aci-dente nuclear em Fukushima, com o com-prometimento dos reatores nucleares da Central Nuclear da cidade. Acreditava-se que as empresas japonesas não estariam de portas abertas para receber visitantes. Porém, o grupo que participou da 40ª Missão de Estudos da Qualidade e Produtividade do IMAM ao Japão, no período de 14 a 26 de outubro, foi muito bem recebido. Foram 16 executivos brasileiros que viajaram ao País com o intuito de visitar empresas “benchmark” em diversos setores de atuação, coordenados pelo diretor da IMAM, José Mauricio Banzato, e pelo gerente de projetos do IMAM, Sidney Rago. Durante a realização da Missão, que percorreu 14 empresas localizadas nas cidades de Osaka, Nara, Kyoto, Nagoya e região de Tóquio (Yokohama), o grupo nada ouviu nem presenciou que remetesse à catástrofe. O tema não foi assunto entre os japoneses nas empresas visitadas e mesmo em Tóquio, centro de mídia do País, nada era veiculado sobre o tema. O que se viu foi organização, simplicidade e disciplina em lições que você lê a seguir: Panasonic E certamente está no “caminho certo”, pois toda a sua filosofia está baseada no desenvolvimento sustentável. A empresa possui até um projeto-piloto (em parceria com algumas outras companhias) a ser im-plementado em 2014 na cidade de Fujisawa (a 50 km de Tóquio) que contempla o geren-ciamento de toda a energia da cidade com base em práticas e tecnologias sustentáveis.
Centro Tecnológico da Sharp Conhecemos toda a evolução da empresa, desde a primeira “invenção” do seu funda-dor, Tokuji Hayakawa, que criou a lapiseira, ou “o lápis que está sempre apontado”, em inglês “ever sharp pencil” (daí a origem do nome da empresa) passando por diversas criações, como rádios, calculadoras e TVs portáteis, até chegarmos aos produtos de hoje, de última geração, como a TV LCD, que, além das três cores primárias que compõem a tela (vermelha, verde e azul), incorporou também a cor amarela, criando uma imagem de nitidez impressionante.
Acompanhamos as operações logís-ticas do local, desde o recebimento dos componentes, passando pela separação, preparação de cargas e expedição dos itens, executados de forma planejada, organizada e em um ritmo acelerado. São cerca de 200 veículos expedidos diariamente, o que equivale a um veículo a cada quatro minutos e uma cobertura média de estoque de duas a três horas. O mais interessante é que pudemos observar a quebra de dois paradigmas: o primeiro é que o CD opera sem auto-mação, tudo é feito e controlado manu-almente, por operadores terceirizados (num total de 70 funcionários operando em dois turnos) exceto alguns transpor-tadores de rolos no piso. Já o segundo paradigma quebrado pela Toyoda Gosei é que ela deixou de utilizar o sistema “milk run”, tão adotado pelas empresas de autopeças para otimizar a ocupação de seus veículos devido ao grande volume de itens movimentados, algo em torno de 40.000 SKUs. Toyota Após uma apresentação breve da história da empresa, fomos visitar o pro-cesso de soldagem dos carros feito por robôs (são cerca de 500 robôs operando) e parte da linha de montagem, onde veri-ficamos “in loco” os dois grandes pilares que compõem o STP: o Jidoka (autonoma-ção com toque humano) e o Just in Time (JIT), e suas ferramentas, tais como o Kanban, Sistema Andon, Poka Yoke, etc. Muratec Makita Na visita às suas instalações, conhece-mos “in loco” as linhas de montagem das ferramentas e suas células de manufatura ergonomicamente proje-tadas, com estoques reduzidos, setups rápidos e colaboradores extremamente concentrados em suas atividades, o que garante a produtividade necessária para a empresa enfrentar seus con-correntes mundiais e manter-se sólida no mercado. Mazak Outro grande projeto da empresa é a construção no Japão de uma fábrica subterrânea, que terá como temperatu-ra constante algo em torno de 15 graus Celsius, o que economizará consideravel-mente o consumo de energia no resfria-mento de ar no verão e aquecimento no inverno, contribuindo para a abordagem sustentável da empresa. Ichiei Kogyo SMC A SMC tem 30% do market share mundial no segmento de componentes pneumáticos e 60% do market share do mercado japonês. No Brasil, a empresa é representada pela SMC Pneumáticos do Brasil, com uma planta situada em São Bernardo do Campo. Komatsu A empresa aplica um forte programa de controle da qualidade em todas as etapas de suas atividades, garantindo a qualida-de dos produtos da marca. Visitamos as linhas de montagem de empilhadeiras e de equipamentos para construção, como pás carregadeiras e tratores, onde verificamos os conceitos do sistema lean manufacturing aplicados, e com todas as atividades visando à sustentabilidade.
A planta fica situada na cidade de Gotemba, a uma hora de distância de Tóquio e aos “pés” do Monte Fuji. Por esse cenário, já percebemos logo na en-trada a preocupação da empresa com o meio ambiente, fato que foi confirmado durante nossa visita. A empresa investe em um forte programa ambiental, man-tendo em suas instalações um lago para captação de água de chuvas, uma área preservada onde vivem alguns animais, e realiza o tratamento de todos os efluen-tes industriais, reciclagem de materiais e geração de energia. Visitamos a área de produção e montagem das máquinas, com proces-sos altamente planejados e produtivos, e com profissionais muito qualificados na habilidade de manuseio e montagem. Tanto na Ricoh como na Mazak, alguns AGVs (“automated guided vehicles”, ve-ículos automaticamente guiados) foram desativados, aumentando a flexibilidade homem sobre a máquina. Bridgestone A empresa é fabricante de pneus para automóveis, caminhões, aviões (in-clusive o pneu para o novo modelo 787 da Boeing), veículos industriais, equipa-mentos agrícolas, veículos utilizados na construção civil e na mineração. Fabrica também amortecedores de borracha uti-lizados em estruturas antiterremotos e filmes de proteção para células solares. No Japão, a empresa tem dez unidades fabris e, em todo o mundo, são um total de 187 fábricas, distribuídas em 25 pa-íses, inclusive a ex-Firestone no Brasil. A empresa também investe em uma abordagem ecológica, com a produção dos pneus Ecopia, que, devido à alta eficiência no desempenho, reduzem o consumo de combustíveis. Seu prédio é todo revestido por placas voltaicas que captam energia solar, armazenando-a e transformando-a em energia elétrica. Visitamos toda a área de produção dos pneus e, ao final da visita, fomos pri-vilegiados por assistir a três verdadeiras “aulas” sobre TQM (Gestão da Qualidade Total), Melhoria Contínua – Kaizen e TPM (Manutenção Produtiva Total). Finalizo resumindo uma frase dita pelo coordenador técnico desta Missão, Sidney Rago: “o Japão continua sendo o templo da produtividade e da melhoria contínua e daqui a alguns anos se tor-nará o templo das empresas verdes. Todas, sem exceção, estão investindo pesadamente em fontes de energia alternativas, economia de energia elétrica, redução na emissão de CO2e melhores práticas ecológicas. Nesta missão pudemos observar a evolução das empresas em relação às missões passadas, com fábricas cada vez mais impecáveis, distâncias percorridas cada vez menores, com determinadas empresas já competin-do por centímetros de manuseios em postos de trabalho, eliminando perdas com movimentações de materiais (antes automatizadas), e automatizando opera-ções onde se agrega valor, ou seja nas operações produtivas. Uma viagem como esta, ao Japão, é certamente uma rica experiência pro-fissional e pessoal. Conhecemos um país encantador, que se supera a cada adversidade que a Natureza lhe impõe, e um povo extremamente educado, gentil, organizado e dedicado a tudo que faz. Até a próxima missão em ou-tubro de 2012. |
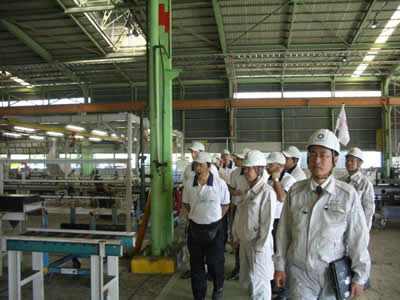